eNews 2022
Research|Penn State - Mission Critical
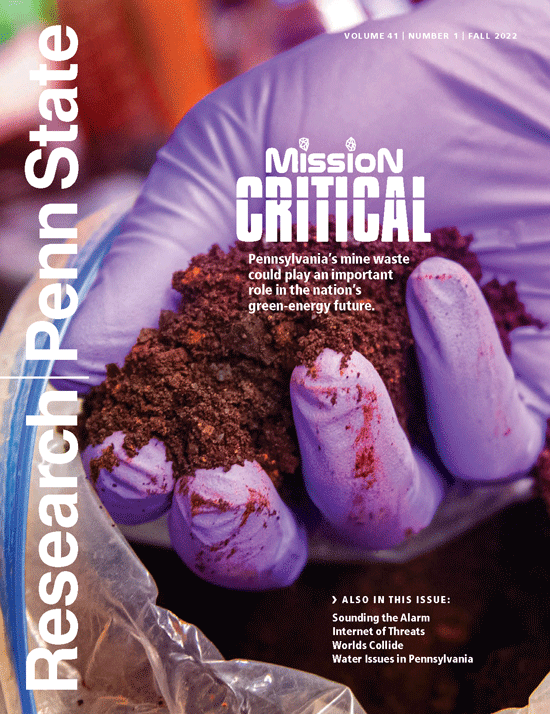
They aren’t called ‘critical minerals’ for nothing.
Think of any technology that’s part of a clean-energy economy: electric vehicles, wind turbines, solar panels. Think of the devices we depend on for work and play: smart phones, computer hard drives, flat screen monitors, rechargeable batteries. Or the systems that undergird our national defense: lasers and missile guidance, radar and sonar.
All of these depend on critical minerals
The U.S. Geological Survey currently designates 50 minerals as critical to the U.S. economy or its national security or both. That number includes the so-called rare-earth elements—the 15 lanthanide metals at the bottom of the periodic table plus scandium and yttrium—along with the battery metals lithium, cobalt, nickel, and manganese, as well as platinum, aluminum, and graphite, among others.
With the accelerating shift toward renewable energy, need for these materials is rising sharply. By 2030, according to Bloomberg, demand for nickel and aluminum will increase 14-fold, with graphite and lithium not far behind.
Read more by downloading pdf or read more online.
New process developed to extract high purity rare earth element oxides
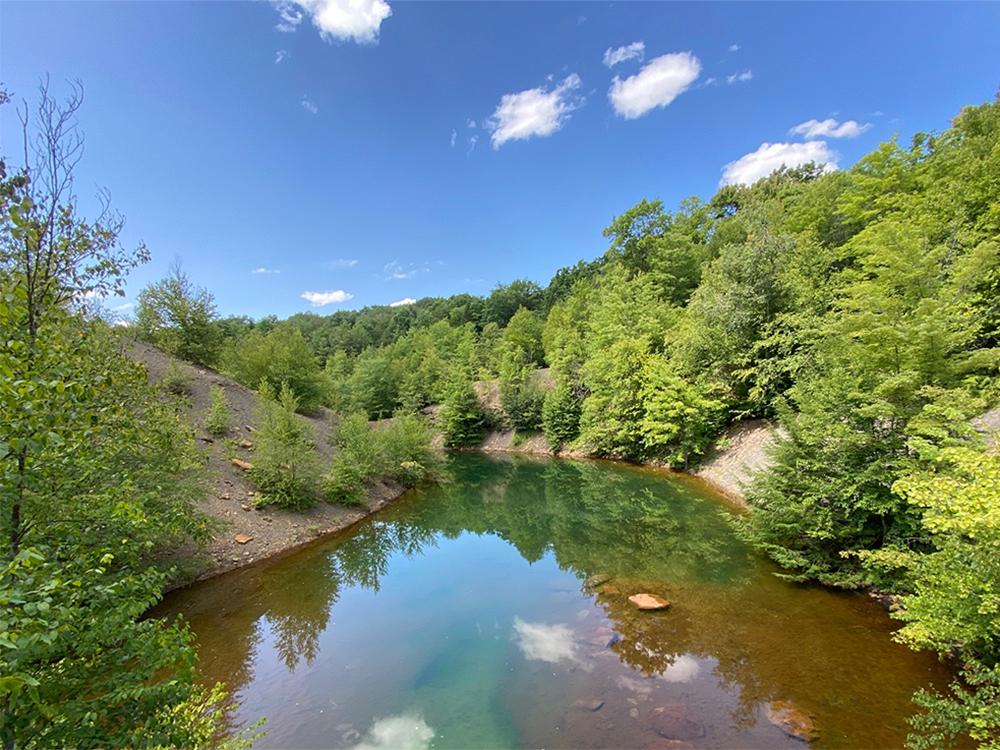
UNIVERSITY PARK, Pa. — Critical minerals, including rare earth elements, are used to power devices like smartphones and computers and are essential to our nation’s economy and national security. Penn State’s Center for Critical Minerals has developed a new purification process that extracts mixed rare earth oxides from acid mine drainage and associated sludges at purities of 88.5%
Critical minerals (CMs), including the 17 rare earth elements (REEs), are used in many common household products like smartphones and computers, and in many commercial products such as electric vehicles, batteries and solar panels. Demand for them has skyrocketed, and they are classified as critical because they have high economic importance, high supply risk, and their absence would have significant consequences on the economic and national security of the United States.
Acid mine drainage (AMD) and associated solids and precipitates resulting from AMD treatment have been found to be viable sources of multiple CMs, including REEs, aluminum, cobalt and manganese.
The U.S. Department of Energy (DOE) has funded efforts to demonstrate both the technical feasibility and economic viability of extracting, separating and recovering REEs and CMs from U.S. coal and coal by-product sources, with the goal of achieving mixed rare earth oxides from coal-based resources with minimum purities of 75%.
“We have been working to develop strategies to recover CMs and REEs from these waste streams and have achieved a milestone of 88.5% grade REEs,” said Sarma Pisupati, professor of energy and mineral engineering and director of the Center for Critical Minerals at Penn State. “The current target set by the DOE for achieving mixed rare earth oxides is 75% and we have surpassed that target.”
Acid mine drainage and associated sludge material representing the Lower Kittanning coal bed were obtained from three treatment sites operated by the Pennsylvania Department of Environmental Protection and were characterized and evaluated for recovery of multiple critical minerals.
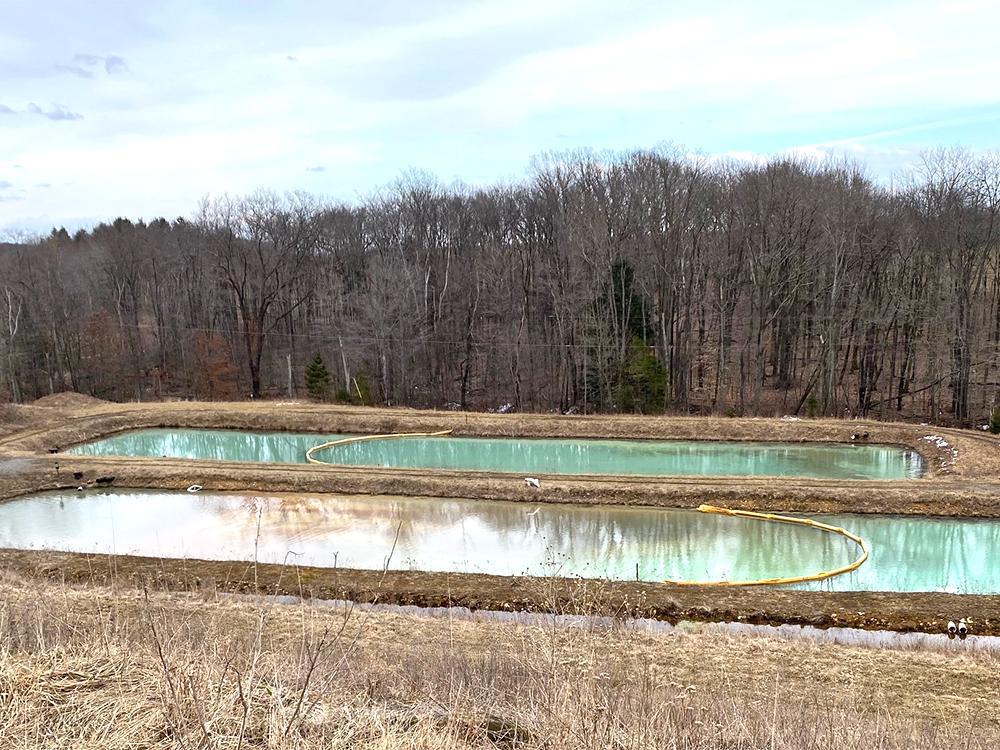
A novel purification process, based on a previously developed three-stage AMD treatment process, was designed to recover high-grade aluminum, REE, cobalt and manganese products from the sludge materials through aqueous processing with multiple cleaner steps and precise control of the process parameters, according to the researchers.
“The extraction of REEs and CMs directly from AMD eliminates the need for the dissolution of sludge and associated costs of reagents and processing, resulting in more sustainable waste disposal practices with low cost,” said Mohammad Rezaee, assistant professor of mining engineering at Penn State and co-author on the study. “We have demonstrated that we are able to turn these waste streams, which have been of environmental concerns for decades, into valuable resources, so this is a win-win for the environment, the commonwealth and the nation.”
AMD is typically treated by adding lime or other chemicals to raise the pH to 7.
“Typically, AMD is neutralized through the addition of various alkaline chemicals,” said Rezaee, who also holds the Centennial Career Development Professorship in Mining Engineering. “As the pH of the AMD increases during the treatment process, metals precipitate as metal hydroxides or other complexes.”
In the new system, the pH is still raised to a pH of 7, but in stages.
“Instead of adding sodium hydroxide, calcium hydroxide or lime all at once to raise the pH, we are raising it in stages,” said Pisupati. “The advantage of this method is that it allows certain minerals to precipitate out at different pH levels. If we add in our base all at once and bring the pH to 7, all these things will precipitate at the same time. Then we would need to go back and separate them.”
The researchers raised the pH to the level needed for iron to precipitate and then to the pH needed for aluminum to precipitate. After iron and aluminum are removed, REEs are recovered through carbonate precipitation, according to the researchers.
“Our challenge was that we could not get 100% of the iron and aluminum removed; there was a little bit of residue in the REE concentration,” said Pisupati. “Even if you have only 1% of aluminum content in the mixture it dominates, and your quality of rare earths will not be as pure. This was addressed in the new purification process.”
In the purification process, precipitates that were removed are put back though the cycle to remove iron, aluminum and other residues.
“In the purification process, we go through the cycle all over again, going back to a pH of 3 or 3.5 and starting all over,” said Pisupati. “We are getting rid of the other residues slowly, maybe two times or three times through the cycle, to increase the REE purity. In our previous research we were at about 17% to 18% grade, so this is a significant accomplishment.”
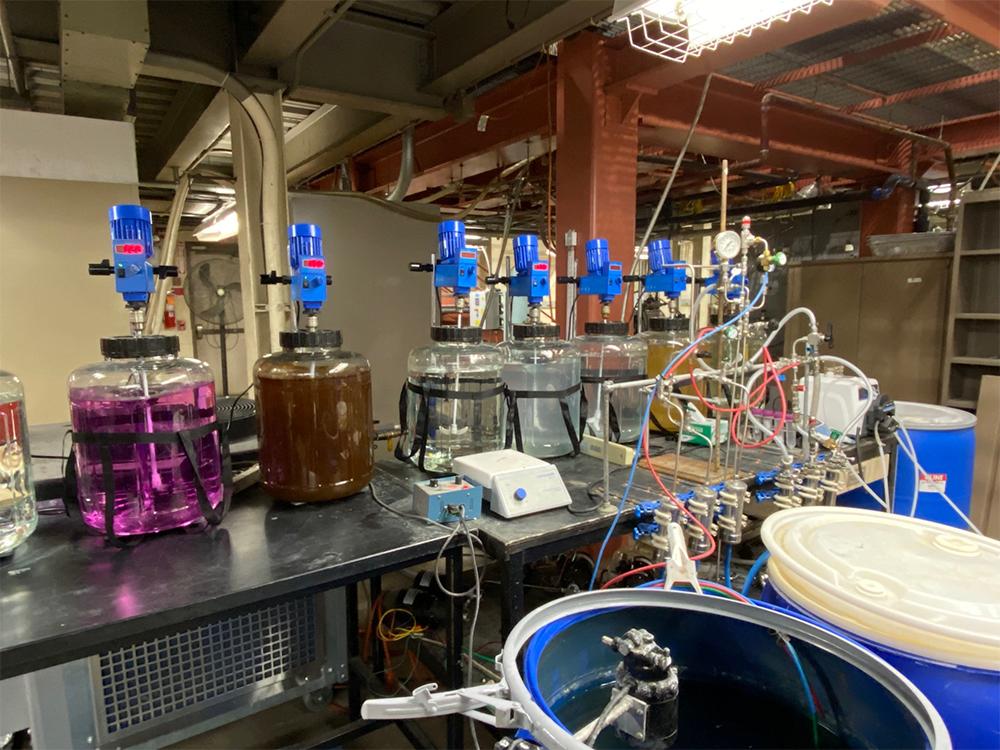
Recoveries of more than 99% for the target elements were achieved with the design of a recycling load. In the original three-stage precipitation process, the cobalt and manganese precipitates had a concentration of 0.85% and 23%, respectively. As a result of the purification process, their concentrations were increased to 1.3% and 43%, respectively. The scientists reported their findings in Minerals Engineering.
Behzad Vaziri Hassas and Younes Shekarian, both graduate students in energy and mineral engineering, also participated in this research.
Geoscientist enjoys critical mineral successes at national lab
UNIVERSITY PARK, Pa. — Penn State alumna Christina Lopano works at the National Energy Technology Laboratory (NETL), which is one of the three applied research labs among the 17 national labs operated under the Department of Energy (DOE). So, she said, she’s used to seeing the results of her work called upon for application in real-world settings.
But the massive push for extracting rare earth elements (REEs) from mining and energy-based waste products is something even she couldn’t have foreseen.
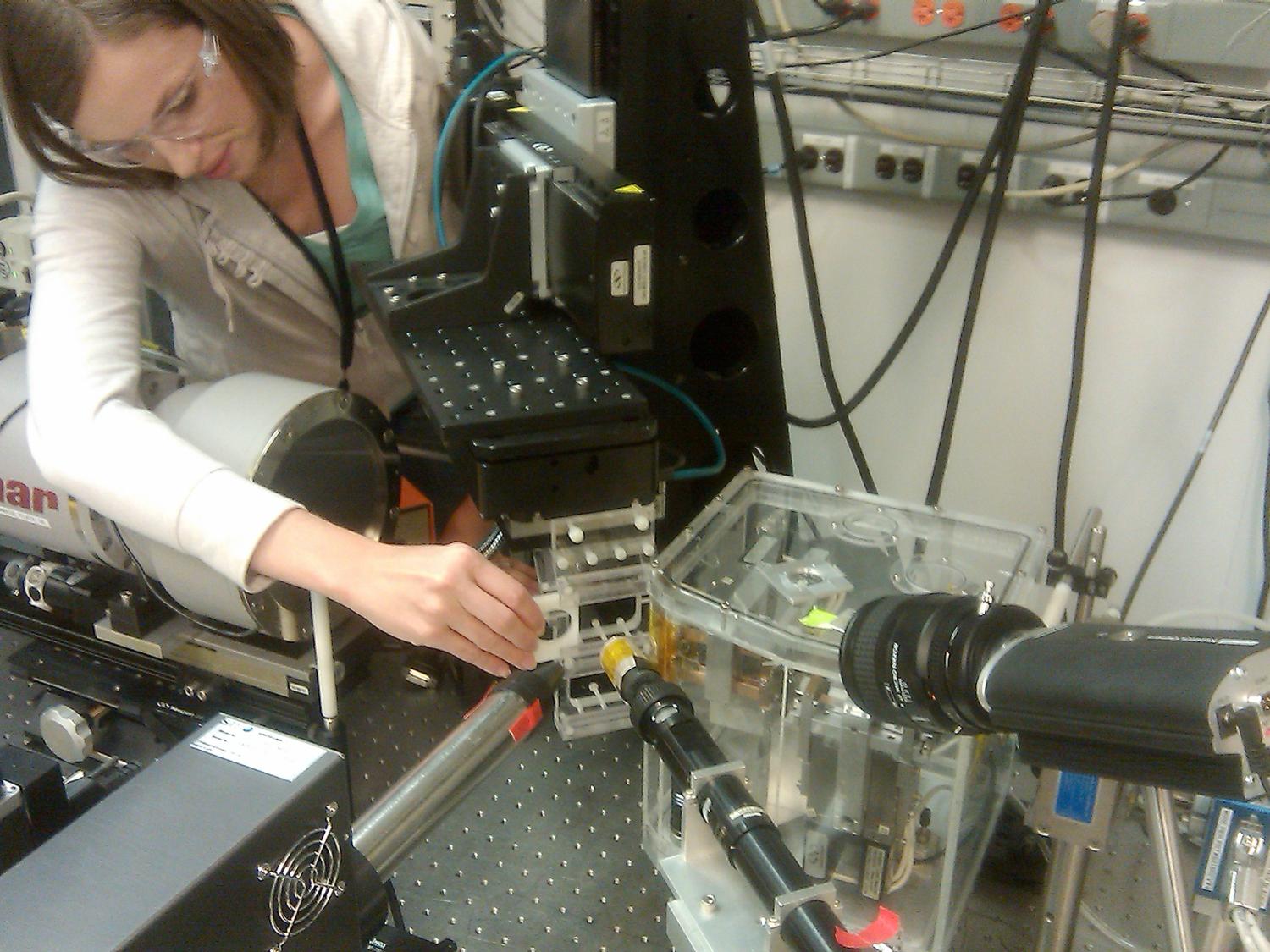
“It’s very interesting when the research you do becomes such a hot topic,” Lopano said.
Lopano, who earned her doctoral degree in geosciences from Penn State in 2007, has for several years been researching ways to unbind metals used in a range of electronics and other critical devices such as batteries, cellphones and vehicles. REEs — which are part of a larger group of critical minerals — are deemed critical because of the nation’s necessity for them as well as a reliance on foreign powers for importing them. Penn State launched a critical minerals consortium in 2021 and began the Center for Critical Minerals in 2019.
Her research improved technology for recovering REEs by incorporating advanced imaging and spectroscopy techniques coupled with laboratory geochemistry to develop methodologies for removing the elements from coal waste byproducts. It earned Lopano the Secretary of Energy’s Excellence Award.
“These awards are among the highest department honors a federal employee or contractor can receive,” NETL Director Brian Anderson said. “With her background in mineralogy, Dr. Lopano has long been on the leading edge of geoscience research, and her work has made significant contributions in NETL’s efforts to find solutions to clean our water and air, lower the environmental footprint of energy production and help communities in need of new jobs and industries. We’re fortunate to benefit from her expertise. She stands out as a driver of meaningful change.”
Pennsylvania Stakeholders Participate in Critical Minerals Meeting
FOR IMMEDIATE RELEASE – March 21, 2022 (HARRISBURG, PA) - - Stakeholders met via Zoom, hosted by the Pennsylvania Manufacturers’ Association, to learn about and discuss the role of the critical minerals industry as it develops in the United States and specifically in Pennsylvania.
The summit brought together national industry experts, state lawmakers and staff, and private sector stakeholders to consider the national dialogue regarding the critical mineral supply chain and how this sector presents a strategic opportunity that is unique to the commonwealth. Highlighted were recent federal initiatives, waste reclamation-to-mineral sourcing, and the consideration of industry best practices to attract project investment.
“Access to critical minerals is essential for our economy, supply chains, national security, and true energy independence,” said David N. Taylor, President & CEO of the Pennsylvania Manufacturers’ Association. “Pennsylvania can be a part of the solution to our foreign dependence problem if state government joins us as a partner in this process.”
“If Americans want their smartphones and electric vehicles to be made from materials sourced with the world’s strictest environmental standards and worker safety protections, we must increase domestic production of critical minerals and rare earth elements,” said Wayne Palmer, Executive Vice President, Industrial Minerals Association - North America. “The good news is that both political parties are sounding the alarm on the need to reduce our dependency on foreign sources like China and Russia. But rather than impose new regulatory burdens and taxes as some are proposing, policymakers should be facilitating new domestic sourcing, such as improving the timeliness and predictability of federal and state permitting processes.”
DOE will build nation's first large-scale facility to turn fossil fuel waste into rare materials for tech
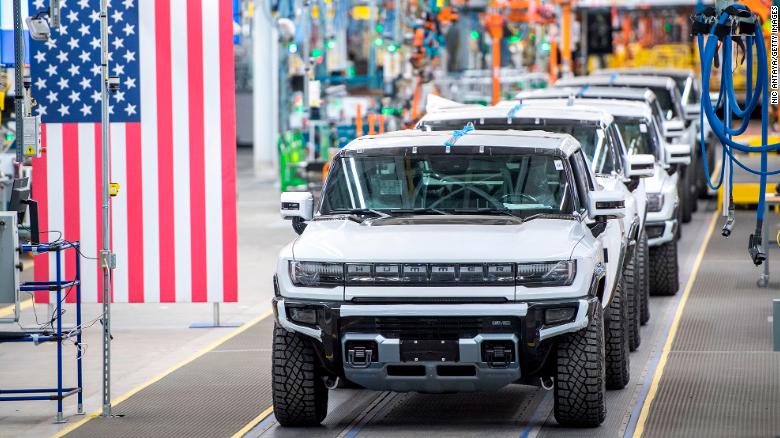
(CNN)-The vast majority of critical minerals and rare earth elements that help power electric vehicles and wind turbines come from mining operations overseas. But a new initiative spearheaded by the US Department of Energy is looking for ways to extract them from fossil fuel waste.
The Energy Department plans to build the nation's first large facility to extract critical minerals like nickel and cobalt from waste like coal ash. Those metals could then be used in components for renewable-energy batteries, cell phones and electric vehicles, among other technologies.
On Monday, the department is releasing a request for information from industry, developers and research institutions on how to build and operate the new facility, shared first with CNN.
"Since we get fossil fuels from the earth, there's a lot of other components other than just the carbons," Jennifer Wilcox, the principal deputy assistant secretary for the Department of Energy's Office of Fossil Energy and Carbon Management, told CNN. "There's critical minerals like cobalt and nickel, and there's also rare earth elements."
As demand for critical minerals surges, the US is at a supply-chain disadvantage for them. The US currently imports more than 80% of its rare earth elements from offshore suppliers. Much of its critical mineral supply needed to power batteries is also shipped from overseas.
China in particular has cornered the global market on processing critical minerals and rare earth elements, but countries including Australia and Malaysia are also involved. Department of Energy officials like Wilcox see coal waste as a new opportunity to make the US less reliant on foreign supply.
Even so, it will take years to realize this vision. The new facility -- which the department plans to construct by 2026 and have operational by 2028 -- will both refine materials and show private industry how to scale up extraction of rare earth elements and critical minerals from used fossil fuels.
The department aims to have the facility be able to process about 1,000 metric tons of mixed rare earth oxides, increasing that to 10,000 metric tons per year by 2035 and 20,000 metric tons per year by 2040.
And although foreign countries lead the US in processing critical minerals from mining, this concept of processing fossil fuel waste for minerals is a relatively new and untested one.
"I think we are really in the lead on these concepts," Wilcox said.
Focusing on coal waste
As the US tries to build out its domestic mining supply, it should also pursue secondary sources of obtaining the material, said Sarma Pisupati, an energy professor and minerals expert at Penn State University.
"We need to find domestic sources, and secondary sources are important to look at," said Pisupati. "These are coming from waste piles particularly. If we can develop the technology, we can clean up the environment as well as get these resources."
The project will primarily focus on extracting minerals from coal waste. However, byproducts from oil and gas drilling -- such as the water used to extract the fuel -- can also be good sources of minerals like lithium.
"This is really focused on coal, but it doesn't mean that what we learn from the chemical, physical, thermal extraction processes we're investing in -- that they can't also be applied to other energy resources as well," Wilcox said. "That's what we would like to see in the future."
Green, bio-based extraction of rare earths from domestic ores for a sustainable world
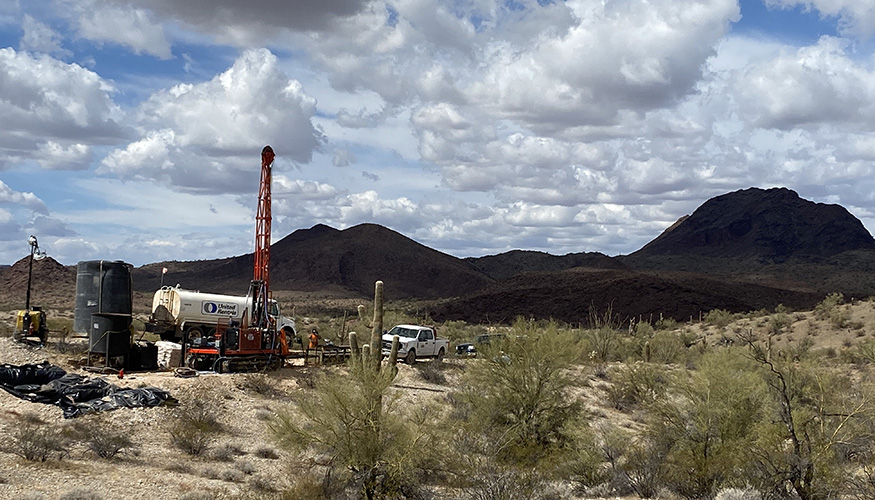
Lawrence Livermore National Laboratory (LLNL), Penn State (PSU) and University of Arizona (UA) researchers are partnering with industry collaborator Western Rare Earths (WRE), U.S. subsidiary of American Rare Earths Limited, to use a naturally occurring protein to extract and purify rare earth elements (REEs) from abundant, domestic ore-based feedstocks and waste materials without harming the environment. It could offer a new avenue toward a more diversified and sustainable REE sector for the United States.
Domestic sourced and processed REEs are essential for American competitiveness in the clean energy and high-tech industries. These rare earth and other critical minerals are used in many devices vital to a high-tech economy and national security, including computer components, high-power magnets, wind turbines, mobile phones, solar panels, superconductors, hybrid/electric vehicle batteries, LCD screens, night-vision goggles and solid oxide fuel cells (SOFCs). To date, the chemical processes used to extract, separate and purify REEs are harmful to the environment and not sustainable.
In the project, funded by the Department of Energy's Critical Materials Institute, the researchers turned to the protein lanmodulin, which PSU's Center for Critical Mineralsteam member Joseph Cotruvo discovered. This discovery enabled a one-step quantitative and selective extraction of REEs from electronic waste and pre-combustion coal — capabilities that other chemical extraction methods do not offer.
Through a collaborative effort between LLNL, PSU, UA and WRE, the team plans to develop a scalable, all-aqueous, protein-based method for high-purity recovery of the REEs scandium and yttrium from low-grade, abundant domestic allanite ore. Yttria-stabilized zirconia (YSZ) is the most widespread electrolyte material used for SOFCs, given its high ionic conductivity, electronic resistivity and stability over a wide temperature range. Scandia-stabilized zirconia (ScSZ) is an attractive alternative to the yttrium due to its higher conductivity and excellent stability, allowing lower operating temperatures and improved longevity. Scandium also is used in high-strength, lightweight aluminum–scandium alloys that offer fuel savings when used in aircraft and vehicles.